How to Identify High-Quality LED Grow Lights? In-Depth Analysis of Material Impact on Performance
LED grow lights have become essential equipment in modern agriculture and indoor cultivation. However, product quality varies widely, with 90% of a light’s lifespan, efficiency, and safety determined by material selection. This article analyzes key components—housing, heat sinks, aluminum substrates, wiring, thermal grease, and adhesives—to help you evaluate LED grow light quality.
Table of Contents
- The Top 6 Causes of Plant Scorching
- No. 1 Cause: Excessive Nutrition – 90% of Beginners Over-fertilize
- The Harm of Over-fertilizing
- Tips for Fertilizing Correctly
- No. 2 Cause: High Temperature – The Lethal Effects of High Environmental Temperature
- How High Temperatures Harm Plants
- Effective Ways to Lower Temperatures
- No. 3 Cause: Overheating Lights – The Silent Killer of Scorched Plants
- The Impact of Overheated Lights on Plants
- How to Keep Grow Lights from Overheating
- No. 4 Cause: Prolonged Lighting – How Many Hours Are Safe for Plants?
- Negative Effects of Excessive Light
- How to Control Light Duration Effectively
- No. 5 Cause: Hanging Distance – Are Your Grow Lights Too Close?
- The Risks of Improper Hanging Distance
- How to Adjust Grow Light Distance
- No. 6 Cause: Light Burn: Why Higher PPFD Isn’t Always Better?
- The Risks of Excessive PPFD
- How to Optimize PPFD for Healthy Growth
- Does the Spectrum of LED Grow Lights Cause Plant Burn?
- Conclusion
Housing Material: Aluminum Alloy is the Best Choice
The aluminum housing acts as the armor of the light, providing durability and heat dissipation while protecting internal components. Here are some simple tips for choosing the right housing material.
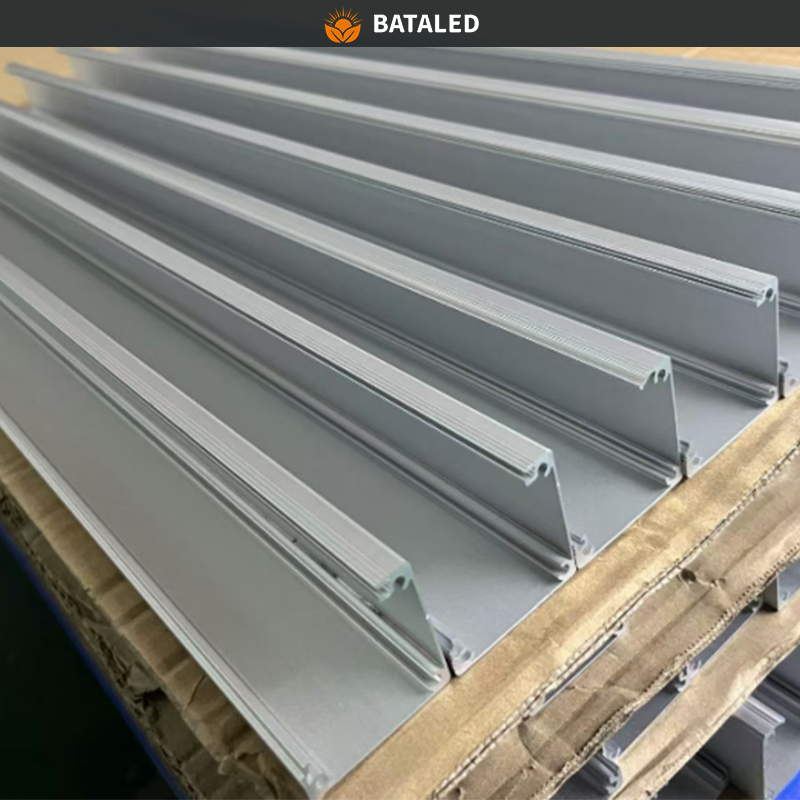
Common materials for LED light housings include aluminum alloy, engineering plastic, and stainless steel. Each has its pros and cons, and the choice depends on specific application needs. Refer to the comparison table below:
Material | Pros | Cons |
Aluminum Alloy | Excellent thermal conductivity, lightweight, corrosion-resistant | Higher cost, lower hardness and strength compared to steel |
Engineering Plastic | Lightweight, low cost, corrosion-resistant, easy to mold | Poor heat dissipation, lower mechanical strength and heat resistance |
Stainless Steel | Extremely corrosion-resistant, high mechanical strength | Poor thermal conductivity, heavy, difficult to process |
Thermal conductivity also varies significantly between materials. Refer to the thermal conductivity comparison table:
Material | Thermal Conductivity (W/(m·K)) |
6063 Aluminum Alloy | 190–210 |
6061 Aluminum Alloy | 151–202 |
ADC12 Die-Cast Aluminum | 85-96 |
Stainless Steel | 14–19 |
High-Thermal Plastic | 15–25 |
Regular Plastic | 1–5 |
Considering all factors, aluminum alloy is the best choice for housing due to its superior thermal conductivity, lightweight, and corrosion resistance.
Aluminum Substrate: How to Choose the Right LED Aluminum Substrate
The LED aluminum substrate acts like the “blood vessels” of the light’s heat dissipation system. If it’s too thin, it may dissipate heat quickly but is prone to bending or deformation. If it’s too thick, heat transfer slows down, reducing the efficiency of the LED chips. To help you choose the right thickness and thermal conductivity for effective chip protection and heat dissipation, here are some recommendations:
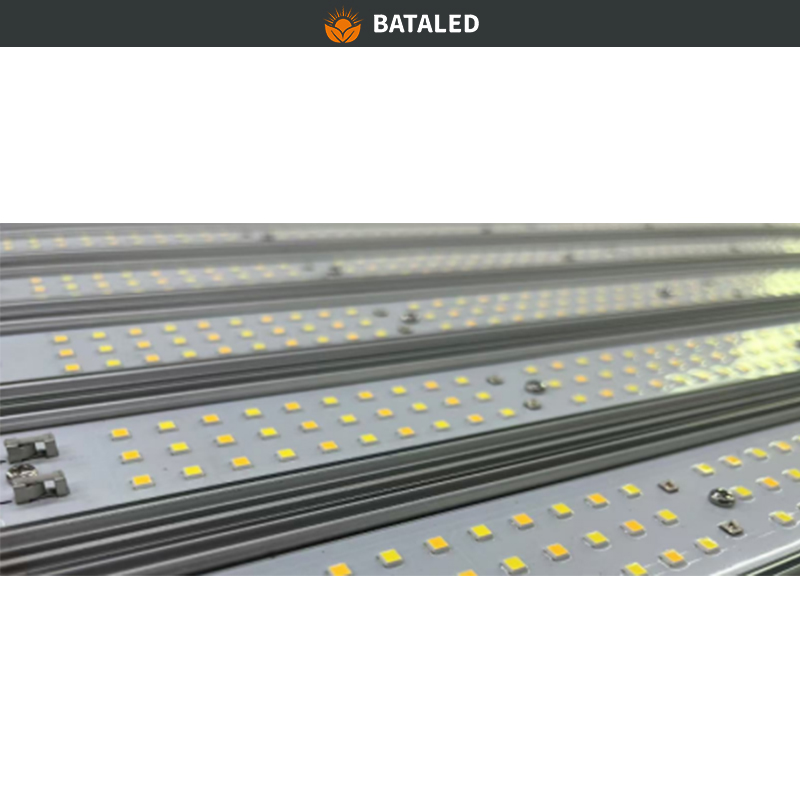
(1) Aluminum Substrate Thickness Selection:
The thickness of LED aluminum substrates typically ranges from 0.5mm to 3.0mm. Generally, thinner substrates have shorter heat dissipation paths and dissipate heat faster. However, if a large amount of heat isn’t transferred to the heat sink in time, thermal expansion and contraction may cause the substrate to bend or deform.
On the other hand, thicker substrates are more resistant to deformation but dissipate heat more slowly, which can lead to heat accumulation and reduced chip efficiency over time. So, how do you choose the right thickness? Refer to my recommended solutions:
Application Scenario |
Recommended Thickness |
Reason |
Low to Medium Power Lights |
0.8-1.5mm |
Prioritize lightweight design while ensuring structural stability (e.g., adding support frames). |
High-Power Lights |
1.5-2.0mm |
Balance heat dissipation and deformation resistance, paired with external heat sinks (e.g., fins or fans). |
Extreme High-Density/High-Temp Environments |
≥2.0mm |
Thicker substrates prevent fatigue deformation from long-term thermal cycles, suitable for industrial or commercial applications. |
(2) Thermal Conductivity Optimization:
The thermal conductivity of an LED aluminum substrate reflects how efficiently heat is transferred from the LED chip through the substrate to the heat sink. Common thermal conductivity values are 1.0, 1.5, and 2.0 W/m·K. Generally, the higher the thermal conductivity, the better the heat transfer. Here’s a recommended combination:
(3) Thermal Resistance Control Strategy:
Thermal resistance (unit: ℃/W) refers to the rate of temperature difference between two surfaces during heat transfer. Lower thermal resistance means a smaller temperature difference between the LED chip and the heat sink, extending the light’s lifespan.
Key strategies to reduce thermal resistance:
- Choose substrates with high thermal conductivity.
- Optimize contact between the substrate and heat sink (e.g., using thermal paste or graphene pads).
- Minimize intermediate layers (e.g., avoid stacking multiple insulating materials).
Heat Sink: Opt for High-Efficiency Aluminum Heat Sinks
When evaluating the heat dissipation performance of LED grow light heat sinks, consider factors such as material choice, structural design, and heat dissipation area. Below is a professional analysis and recommendations:
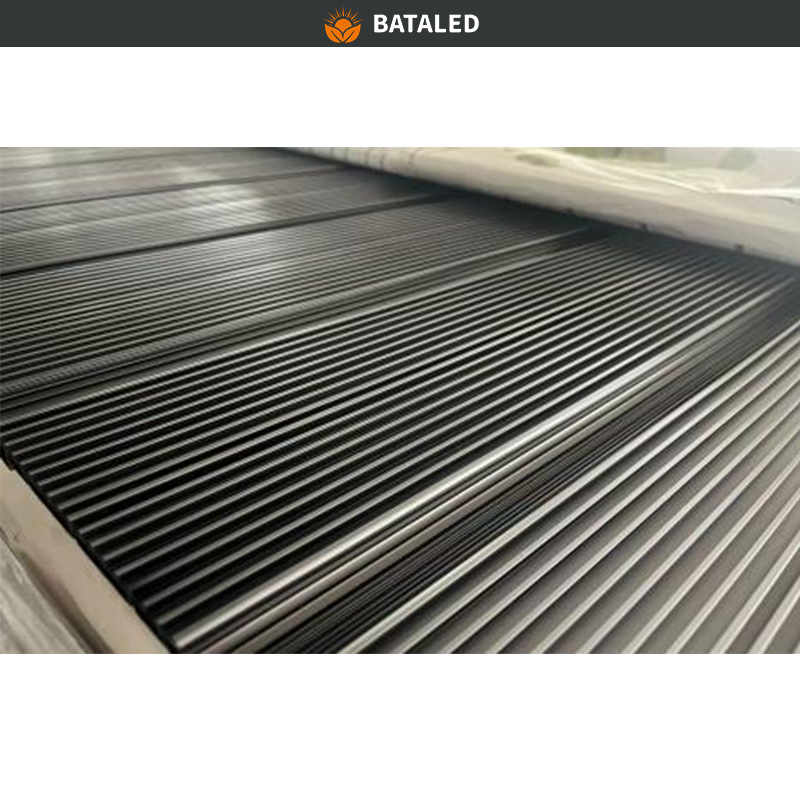
(1) Material Selection:
Common materials for LED heat sinks include aluminum alloy and copper. Each material has its unique advantages and disadvantages, and the choice should be based on specific application needs. Refer to the following material comparison table:
Application Scenario |
Recommended Thickness |
Reason |
Low to Medium Power Lights |
0.8-1.5mm |
Prioritize lightweight design while ensuring structural stability (e.g., adding support frames). |
High-Power Lights |
1.5-2.0mm |
Balance heat dissipation and deformation resistance, paired with external heat sinks (e.g., fins or fans). |
Extreme High-Density/High-Temp Environments |
≥2.0mm |
Thicker substrates prevent fatigue deformation from long-term thermal cycles, suitable for industrial or commercial applications. |
Different materials also exhibit significant differences in thermal conductivity. Refer to the following thermal conductivity comparison table:
Thermal Conductivity |
Application Scenario |
Matching Recommendation |
2.0 W/m·K |
High-power, enclosed environments, multi-LED setups |
Must pair with high-efficiency heat sinks (e.g., copper-based or liquid cooling systems). |
1.5 W/m·K |
Standard grow lights |
Pair with air-cooled heat sinks to meet most needs. |
1.0 W/m·K |
Low-power, intermittent-use lights |
Only for low-cost solutions; strictly control operating hours. |
After considering factors such as heat dissipation performance, corrosion resistance, cost, and weight, although copper offers excellent heat dissipation and corrosion resistance, its weight and price far exceed those of aluminum alloy. Additionally, copper is harder to process and less efficient to manufacture. Therefore, 6063 aluminum alloy heat sinks are recommended.
(2) Heat Sink Structural Design:
- Finned Structure: Increases contact area with air, improving heat dissipation efficiency.
- Airflow Design: Facilitates natural convection or forced air cooling (e.g., with fans).
- Contact Surface Optimization: Ensures tight contact between the heat sink and aluminum substrate, reducing thermal resistance (e.g., using thermal paste or graphene pads).
I recommend BATA LED Grow Light’s finned quantum board series and Spider series, which use aluminum alloy for the body and feature specially designed finned heat sinks to enhance heat dissipation.


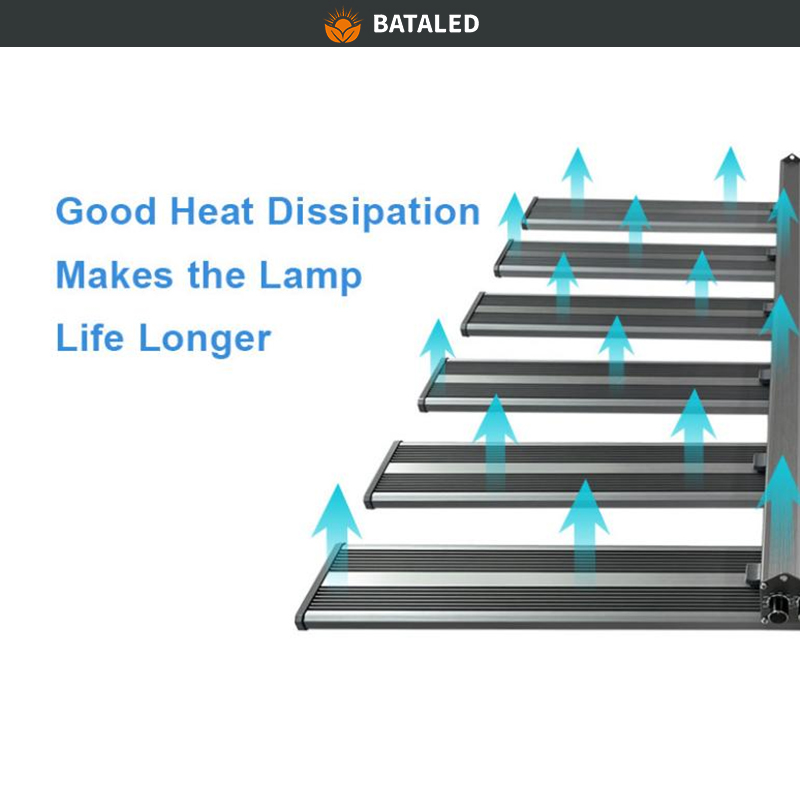
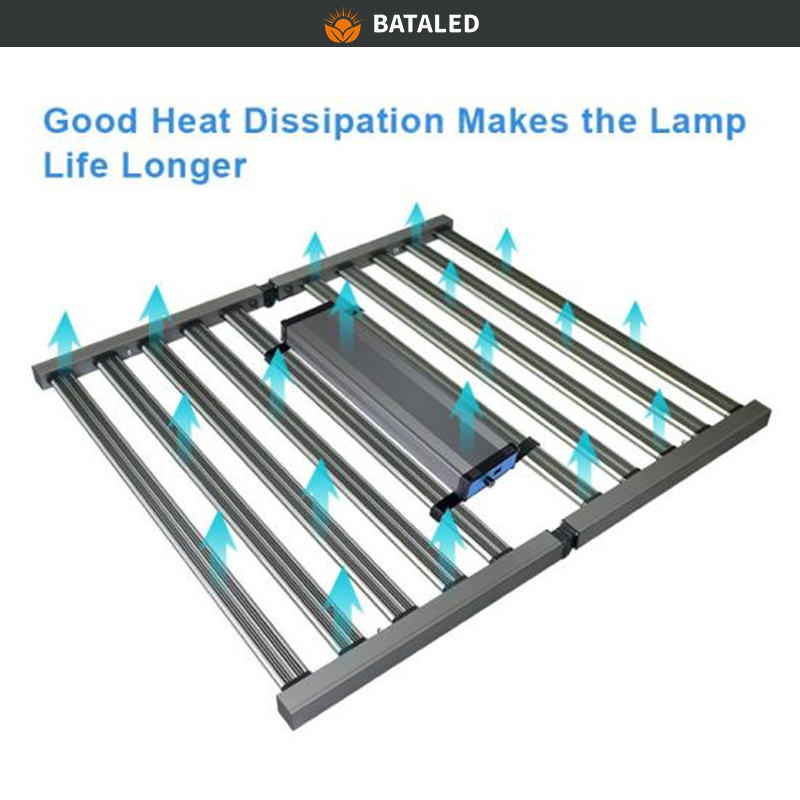
(3) Heat Dissipation Area Optimization:
Larger heat dissipation areas improve heat dissipation.
The heat dissipation area should match the light’s power; higher power requires larger heat dissipation areas.
Reference Formula:
The relationship between heat dissipation area (S) and power (P) can be approximated as:
S=k×P
Where k is an empirical coefficient, typically 100-150 cm²/W (specific values depend on ambient temperature and heat sink design).
Electrical Safety: The Importance of Grounding Design and Compliant Wiring
The Necessity of Grounding Design
High-quality LED grow lights not only perform well and offer high lighting efficiency but also prioritize safety. A grounding design is essential to protect both the light and the grower, preventing accidents.
The grounding wire is a safety measure that prevents electric shocks, equipment damage, fires, and lightning strikes. Lights without grounding wires have a 70% higher risk of leakage, especially in high-humidity greenhouse environments. Therefore, I recommend choosing lights with internal grounding wires, typically yellow-green, connected via brass grounding rings secured with screws.
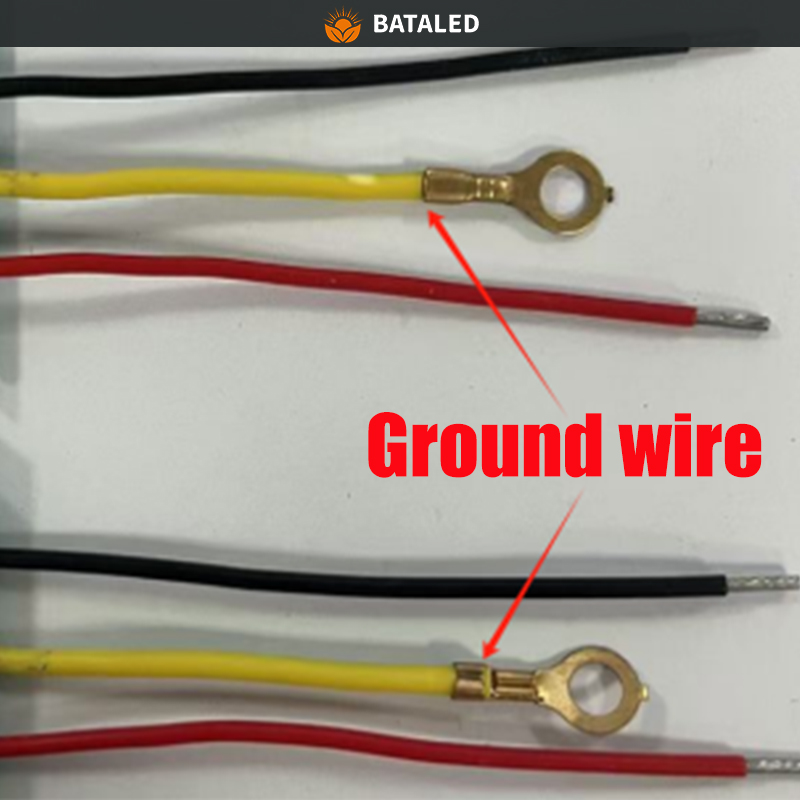
Choosing the Right Wire Specifications
Selecting the right wire specifications ensures stable lighting efficiency and safe operation within specified limits. If the wire gauge is insufficient for the required current, the wires may overheat during prolonged use, potentially leading to burnout. Below are two wire standards:
- Chinese National Standard (RV/RVV): Choose the appropriate wire diameter based on power requirements to ensure safe current ranges.
Chinese standard wires can typically carry 6A per square millimeter. The wire’s outer sheath is marked with size, specifications, model, or certification numbers. For a 1000W light with 220V input, the plug wire should be at least 3-core 0.75mm²; for 48V output split into two lines, each should be at least 2-core 1.5mm².
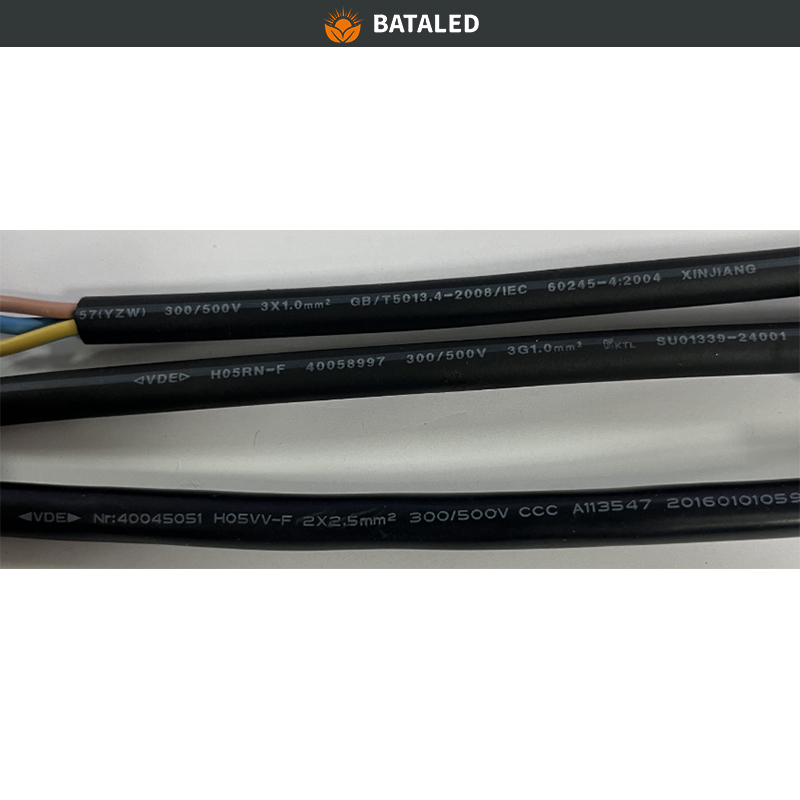
- American National Standard (AWG): Choose the appropriate gauge based on current requirements (higher AWG numbers indicate thinner wires).
AWG (American Wire Gauge) measures wire thickness, with higher numbers indicating thinner wires. American standard wires use PVC or TPU sheathing, with thicknesses ranging from 0.5mm to 1.0mm, offering good pressure and tensile resistance.
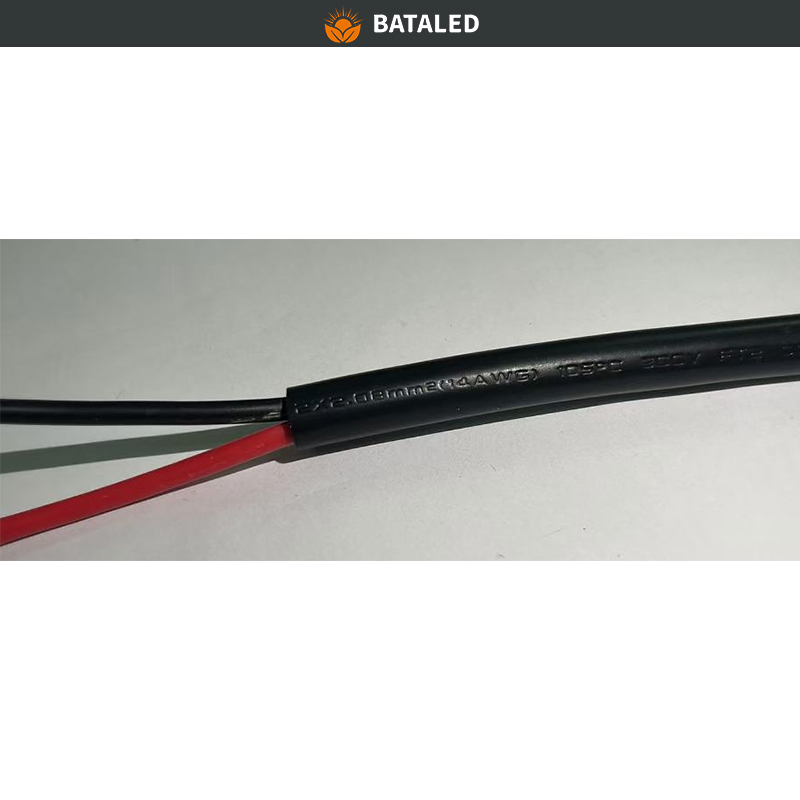
Tip:
Peel back the wire sheath; genuine national standard wires have purplish-red copper cores, while inferior wires often have gray-white cores (copper-clad aluminum). Check the plug’s injection molding; seamless, one-piece designs offer better waterproofing.
Unsung Heroes: Thermal Paste and Coating Adhesives
Choosing the Right Thermal Paste
Thermal paste is characterized by excellent thermal conductivity and electrical insulation. As a heat dissipation material, it fills the gap between the LED chip and the heat sink, improving heat transfer efficiency and preventing LED overheating. LED thermal paste typically has a thermal conductivity of 1.0-5.0 W/m·K, with higher values offering better heat transfer.
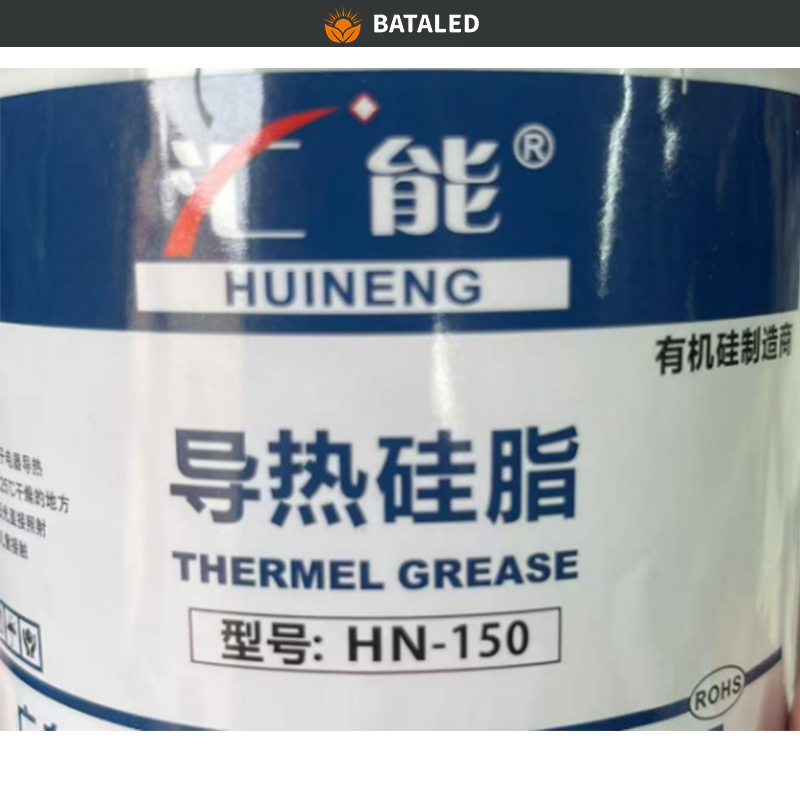
Coating Adhesives
Adhesives are not optional but core materials that determine whether LED grow lights can operate stably in harsh environments. They play a critical role in waterproofing, corrosion resistance, shock resistance, high insulation, and auxiliary heat dissipation. When selecting adhesives, focus on thermal conductivity, weather resistance certifications, and coating precision.
(1) Protection and Certifications:
- Waterproofing and Corrosion Resistance: Adhesives form a 0.1-0.3mm dense protective layer, achieving IP66 protection.
- Shock Resistance: The protective layer absorbs and disperses impacts during transport or installation.
- High Insulation: Adhesives have a volume resistivity >10¹²Ω·cm, preventing leakage in humid environments.
- Auxiliary Heat Dissipation: Some high-thermal-conductivity adhesives (≥1.5 W/(m·K)) can reduce thermal resistance by 5%-10%.
- Compliance Certifications: Choose adhesives with RoHS and UL weather resistance certifications.
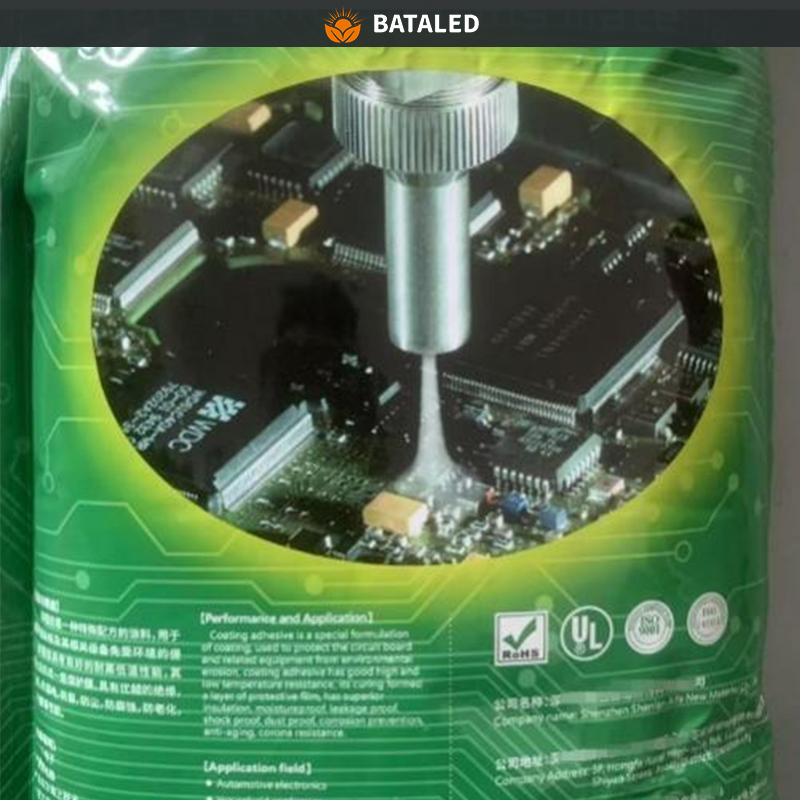
(2) Coating Methods:
- Manual Coating: Requires manual application to the LED surface and solder points.
- Dip Coating: Uses simple equipment to immerse the light board vertically in an adhesive tank for 3-5 seconds.
- Automated Spray Coating: Uses precision spraying instruments to apply a uniform 0.1-0.3mm protective layer.
Comparing the three methods, I recommend choosing manufacturers with precision spraying equipment, like BATA LED, to ensure light quality through reliable instruments and precise processes.
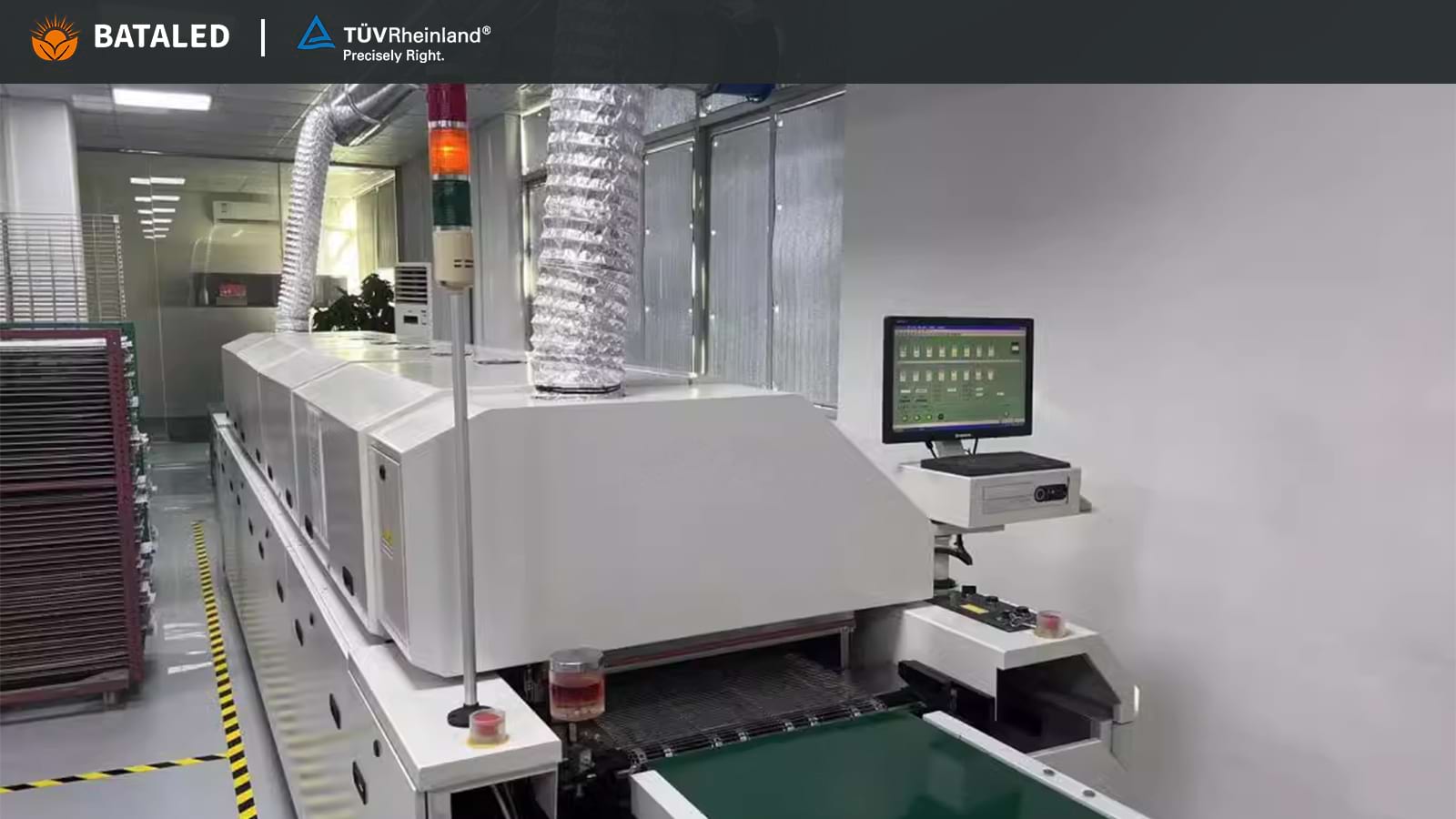
Connectors: The Last Line of Defense for Stable Power Supply
(1) External Waterproof Connectors:
Connectors are essential for stable electrical connections. Choose solid copper pins, especially for high-power LED lights. Given the exposure to water or moisture in cultivation environments, opt for connectors with reliable external waterproof seals, preferably made of nylon (PA66) or PVC.
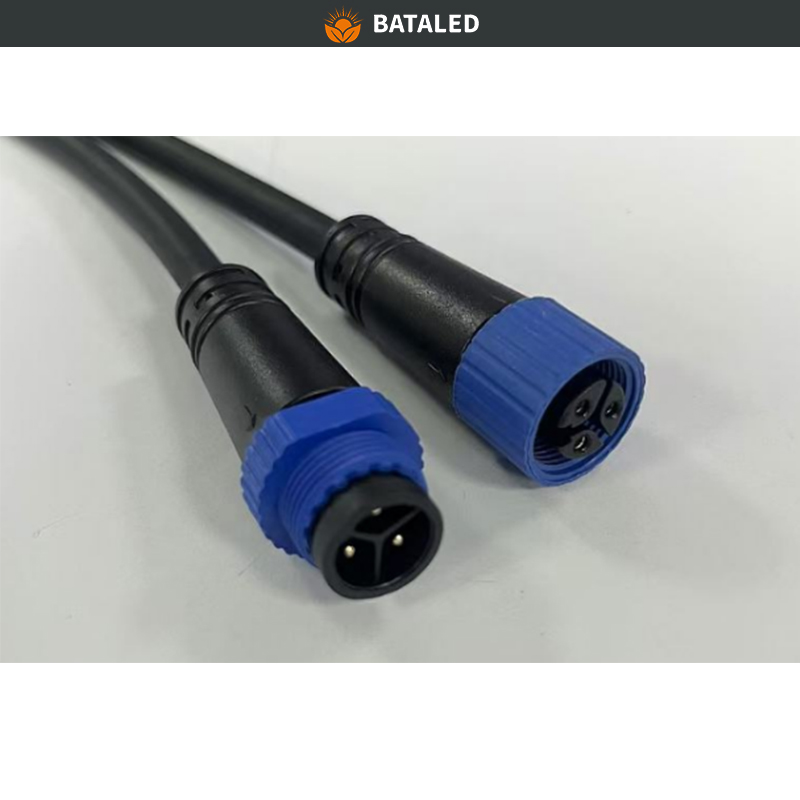
(2) Internal Connection Terminals:
The quality of internal terminals determines the stability and durability of circuit connections. Use terminals with UL, CE, CQC, and RoHS certifications, made of high-quality copper, and avoid overloading.
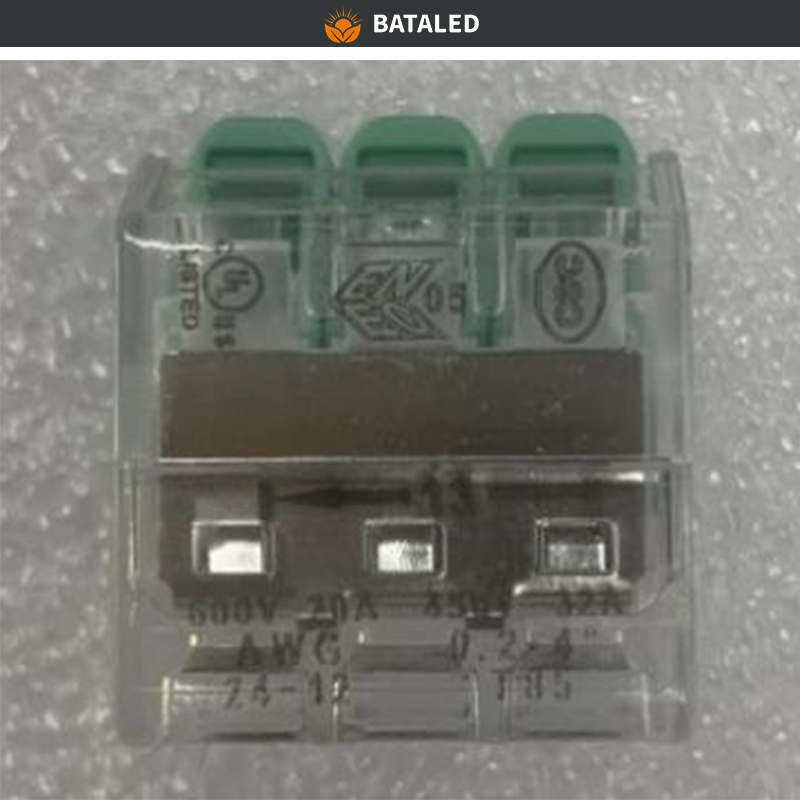
Conclusion
A high-quality LED grow light is the result of material science and precision engineering. Rather than blindly believing marketing claims like “full spectrum” or “high PPFD,” refer to the tips in this article to evaluate the quality of LED grow lights based on core raw materials, from external components like the housing, heat sink, and aluminum substrate to internal elements like wiring, thermal paste, and adhesives.
CATEGORIES
Recommended Post
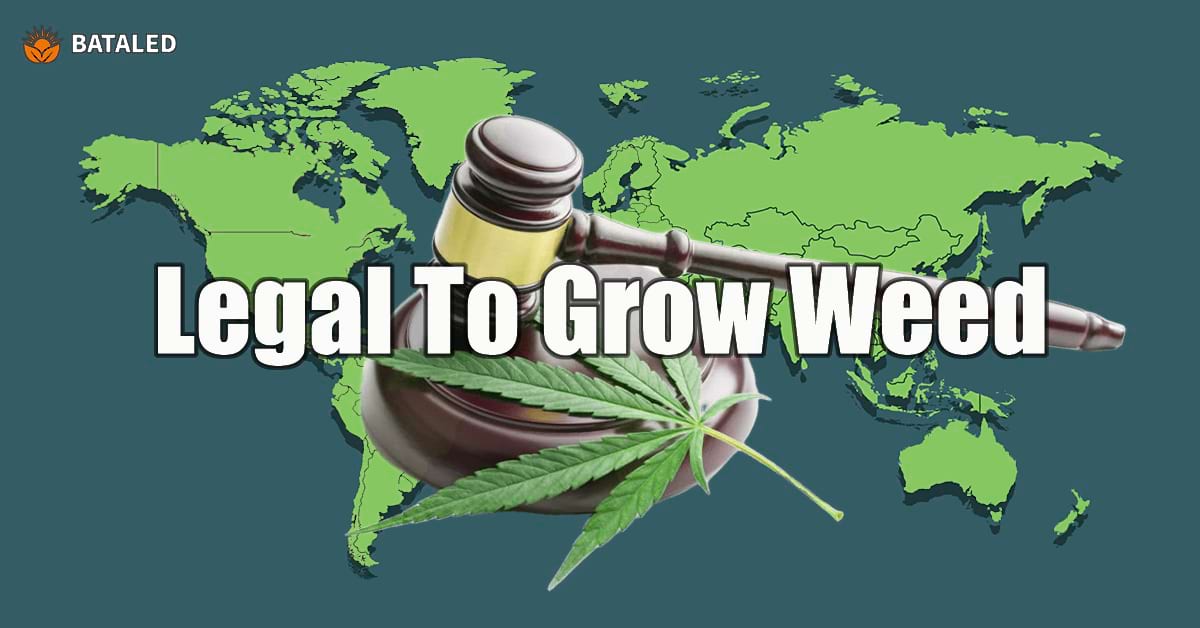
Where It’s Legal to Grow Cannabis: Ultimate Tips & Cultivation Laws
About Author—Jose Li
Jose, a senior content creator at BATA LED, brings over 5 years of expertise in LED grow light. He delivers valuable insights to help growers and farmers better understand LED grow light technology, empowering them to boost crop yields and quality with advanced lighting solutions.
0 Comments